Introduction
This post is based on an excerpt from Circular Transformation of the American Wood Packaging Industry, a master thesis I wrote for the International Institute for Industrial Economics in Lund, Sweden. The work discussed in this article involved developing a tool to calculate the economic and environmental benefits of optimizing wood pallet reuse. Readers will find in-depth information about several best practices for wood pallet reuse found in scientific literature, as well as our own estimates on the cost savings and environmental benefits associated with these best practices.
If you are interested to know more about our project to transform the American wood packaging industry, here are some helpful links:
Wood pallet reuse systems
To understand the importance of wood packaging industry transformation, one must also understand the central role its primary product, the wood shipping pallet, plays in modern supply chains. Pallets are the backbone on which physical supply chains operate, carrying over 80% of all commerce worldwide (Raballand & Aldaz-Carroll, 2005). These ubiquitous products serve several critical functions including product protection, the division of inventory into units, and multiplying the labor efficiency of material handling and logistics processes. Though alternatives to the wood pallet exist, namely the injection-molded plastic pallet, wood pallets comprise over 90% of the American pallet market (Buehlmann et al., 2009) and are consistently found to carry lower costs and environmental burdens than pallets made from alternative materials (Khan et al., 2021; Kočí, 2019).
The American wood packaging industry can be classified into two distinct product-service systems based on the way its core product, the wood pallet, is managed throughout its life cycle:
One-way systems: New pallets are manufactured primarily from low-grade, locally available timber. They are then sold to the consumer. The pallets are laden with goods by the consumer and repositioned until they are finally unladen by the recipient. Informal systems of reuse and repair are facilitated for approximately 16% of pallet users (Michel, 2021), but neither the exact extent of reuse and repair practised in these systems nor the lifespan of a typical one-way pallet is known. Activities in one-way pallet systems are primarily carried out by independent SMEs; over 99% of practicing businesses have fewer than fifty employees (Roy et al., 2016). Comparably little is known to scientific literature about the operations of one-way wood pallet systems as compared to returnable pallet systems. One-way systems, classified as systems in which the pallet user maintains ownership of and responsibility for the product, comprise roughly 88% of the American wood pallet market today (Michel, 2021).

Returnable systems: New pallets are manufactured primarily from structural grade lumber. The pallets are rented to the consumer by a pooler who maintains ownership of a large inventory, or “pool,” of pallets. The pooler is responsible for all activities necessary to provide a consistent supply of usable pallets at each consumer site and collect used pallets from recipients, which may be third parties who receive product on returnable pallets and do not participate in the system directly. Pallets in returnable systems are reused and repaired via the pooler many times before reaching the end of their useful lives (end-of-use), when they are recycled in a concentrated and consistent flow. Organised returnable systems comprise roughly 12% of the U.S. wood pallet market (Michel, 2021) and activities are predominantly controlled by a few large, centralised organisations.
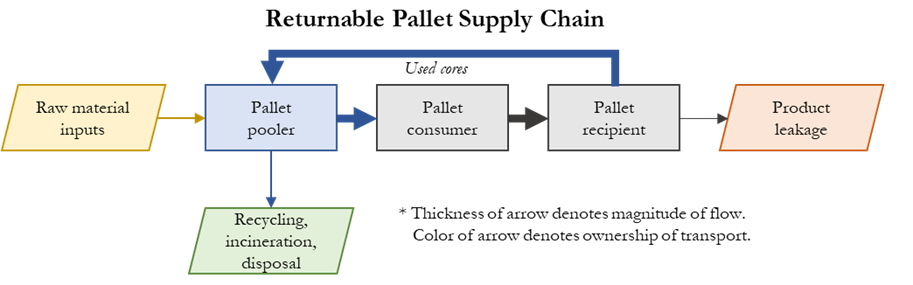
The structure of a returnable pallet supply chain greatly reduces the magnitude of resource inputs and waste outputs related to its function as compared to a one-way pallet supply chain.
How can these returnable systems be made even more efficient?
Best practices from research
The scientific literature points to four main best practces for wood pallet reuse, often resulting in both lower costs and a lower resource burden for wood packaging producers and users.
- Cross-docking: The inspection of used pallets at the dispatch point rather than at the pooling facility so that only damaged pallets must be returned reduces the emissions of returnable block pallet systems by 17-73% depending on loading and handling conditions (Tornese et al., 2016).
- Pre-emptive remanufacturing: The practice of replacing multiple components with a short predicted remaining lifespan at the time a single component must be replaced so that the incidence of damages is reduced and fewer return trips must be made reduces the costs and emissions of the remanufacturing phase of the returnable pallet life cycle by 31-44% and 29-39%, respectively (Tornese et al., 2019).
- Restructuring reverse logistics activities to consolidate returns at the highest point in the buyer’s supply chain via backhaul trips, thus reducing the distances empty pallets travel in between uses, reduced the total truck-km and emissions required to operate a simulated Italian retail pallet supply chain by 65% and 60%, respectively (Accorsi et al., 2019).
- Modifying user behaviour to improve loading and handling conditions and reduce loss rate. One conservative estimate places the contribution of lost and damaged pallets to system emissions at 38% (Bottani & Casella, 2018). Minimising loss and damage rate through better pallet handling practices among users is critical to maximising the resource efficiency of returnable pallet systems.
Modeling the impacts of better pallet reuse
A mathematical model was developed to calculate the per-hire costs, timber consumption, steel consumption, and GHG emissions of five one-way and reusable wood pallet system alternatives at the scale of the individual packaging user using values derived from existing academic and trade literature on transport packaging systems as inputs. The functional unit is the “pallet hire;” which represents either the purchase of one single-use pallet or the rental of one returnable pallet for one use cycle. The system boundary for emissions, timber consumption, and steel consumption begins with raw materials at the new pallet manufacturer’s gate and ends at collection for EOL management.
The five pallet systems modelled in this analysis are based on a hypothetical “typical user” with a demand for 100 48×40” pallets per day, 5 days per week, 50 weeks per year:
System [E]FTL: A one-way pallet system in which a user purchases one-way 48×40” stringer class pallets in weekly full truckload lots (500 pallets per order) delivered by 53’ diesel tractor trailer. The empty pallets reach end-of-life and exit the boundaries of the analysis after one use.
System [E]LTL: A one-way pallet system in which a user purchases one-way 48×40” stringer class pallets in daily less-than-truckload lots (100 pallets per order) delivered by 53’ diesel tractor trailer. The empty pallets reach end-of-life and exit the boundaries of the analysis after one use.
System [R] FTL: Reflective of the current pooled pallet system without optimisation. The user rents FTL lots of returnable 48×40” Grocery Manufacturer’s Association standard block class pallets, the design which is most commonly used in pooling operations in the U.S. All transports are made by 53’ diesel tractor trailer. Handling conditions and loss rate reflect baselines from literature. The pallets are returned to the pooling facility after each use for inspection, remanufacturing, and re-issue. Damaged components are sold to a recycler at a rate of $0.02 per pound and exit the boundaries of the analysis.
System [R+]FTL: Existing pooling practices are optimised using the four best practices identified in Section 2.1. The user rents FTL lots delivered weekly by 53’ diesel tractor trailer. Handling conditions are optimal and loss rate is reduced to 1%. Reverse logistics is also carried out by 53’ diesel tractor trailer in FTL lots. The system boundary remains at sale for recycling.
System [R+]LTL: Existing pooling practices are optimised using the four best practices identified in Section 2.1. The user rents LTL lots delivered daily by 26’ diesel medium duty truck. Handling conditions are optimal and loss rate is reduced to 1%. Reverse logistics is also carried out by 26’ diesel medium duty truck in LTL lots. The system boundary remains at sale for recycling.
Results from the model
Optimized returnable wood packaging systems can carry drastically lower the resource burden of the wood packaging industry. A typical pallet user’s timber consumption can be reduced by up to 90% and their steel consumption can be reduced by up to 98%.
At the same time, operating costs can be reduced by up to 47%. This makes returnable wood pallet systems more cost-effective than one-way pallet systems in many cases, and a natural “low hanging fruit” for packaging users to implement.
The full user-level results are available below. If you are interested in reading about the aggregated benefits of implementing these systems nationwide, read this article.
Bibliography
Related reading
Assessing the prevalence of best practices in the real world
Expanding results to national scale
A model for achieving circularity in the wood packaging industry
Full thesis: Circular Transformation of the American Wood Packaging Industry