Introduction
This post is based on an excerpt from Circular Transformation of the American Wood Packaging Industry, a master thesis I wrote for the International Institute for Industrial Economics in Lund, Sweden. The work discussed in this article involved developing a tool to calculate the economic and environmental benefits of optimizing wood pallet reuse. Readers will find in-depth information about the economic and environmental impacts of improving and expanding wood packaging reuse throughout the United States.
If you are interested to know more about our project to transform the American wood packaging industry, here are some helpful links:
Understanding wood packaging as a sustainability issue
Demand for wood pallets places considerable stress on American forest resources. In the United States and the European Union, the wood pallet and container industry is the largest user of new timber outside of the construction industry, consuming more than one fifth of total industrial roundwood harvests (Gerber et al., 2020; Trends and Perspectives for Pallets and Wooden Packaging, 2016). Meanwhile, the southeastern United States has recently undergone deforestation at a rate four times that of the Amazon rainforest (Forests and Biodiversity, 2015), resulting in a release of sequestered carbon equivalent to 9.2 billion tonnes of CO2 between 2001 and 2021 (Global Forest Watch Data Visualizer, 2022).
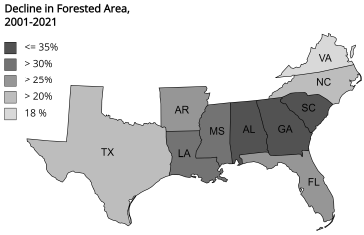
Figure 1‑2. Map of deforestation in the Southern Coastal Plain region of the United States, 2001-2021.
Data source: (Global Forest Watch Data Visualizer, 2022)
One purpose-built reusable wood pallet can replace the function of forty one-way pallets (Bengtsson & Logie, 2015), but as of 2021, only twelve percent of pallet users in the United States participate in organised reuse schemes, citing cost and convenience as major barriers to adoption (Michel, 2021). Displacing the demand for one-way pallets with reusable alternatives would significantly reduce the environmental burden placed on American forests by the wood packaging industry.
Beyond the possibility for reduction of virgin timber demand and its consequential deforestation impacts, there is considerable potential for timber diverted from consumption by a circular transformation of the American wood packaging industry to be used in ways which alleviate other environmental pressures, such as substitution of GHG-intensive materials like steel and concrete in mass timber construction applications.
The European Parliament defines a circular economy as “A production and consumption model which involves reusing, repairing, refurbishing and recycling existing materials and products to keep materials within the economy wherever possible” (Circular Economy [EPRS], n.d.). Circular economy development is driven by a confluence of environmental and economic motivations: It is now common knowledge that we must decouple resource consumption from economic output in order to maintain our current level of economic prosperity without exceeding natural resource constraints.
The circular economy approach to waste management is often conceptualised as a hierarchy of strategies used to minimise waste and resource value loss, with source reduction and reuse being prioritised above recycling and final disposal. This “waste management hierarchy” is a central tenet of waste legislation in the jurisdictions with the most ambitious waste management programmes, most notably the European Union Directive on Packaging and Packaging Waste (“Directive 94/62/EC,” 1995). This circular approach to waste management has shown a significant and positive correlation with economic development while reducing per-capita waste generation in the European Union (Azwardi et al., 2023).
Figure 1-3 below depicts the R-framework for circular economy, which can be applied to the context of wood packaging systems. Practices with a higher position in the chart retain natural resource value more effectively, while those with a lower position result in greater resource value loss. To achieve maximum circularity, systems of production and consumption must be organised so that products and their component materials cascade down this hierarchy in a manner that retains resource value to the greatest degree possible (Russell et al., 2018).
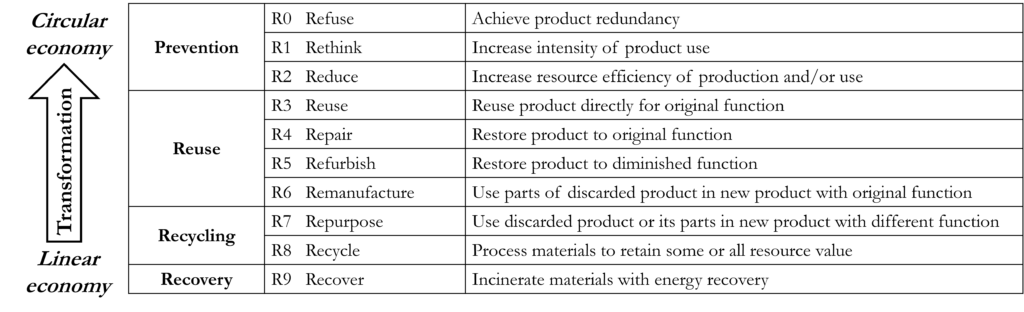
Figure 1‑3. R-framework for circular economy practices.
Information source: (Circular Economy, 2015)
Figure 1-4 below depicts the flow of wood pallet cores, or empty pallets collected at end of use, recovered in the U.S. in year 2016 to their next destinations.
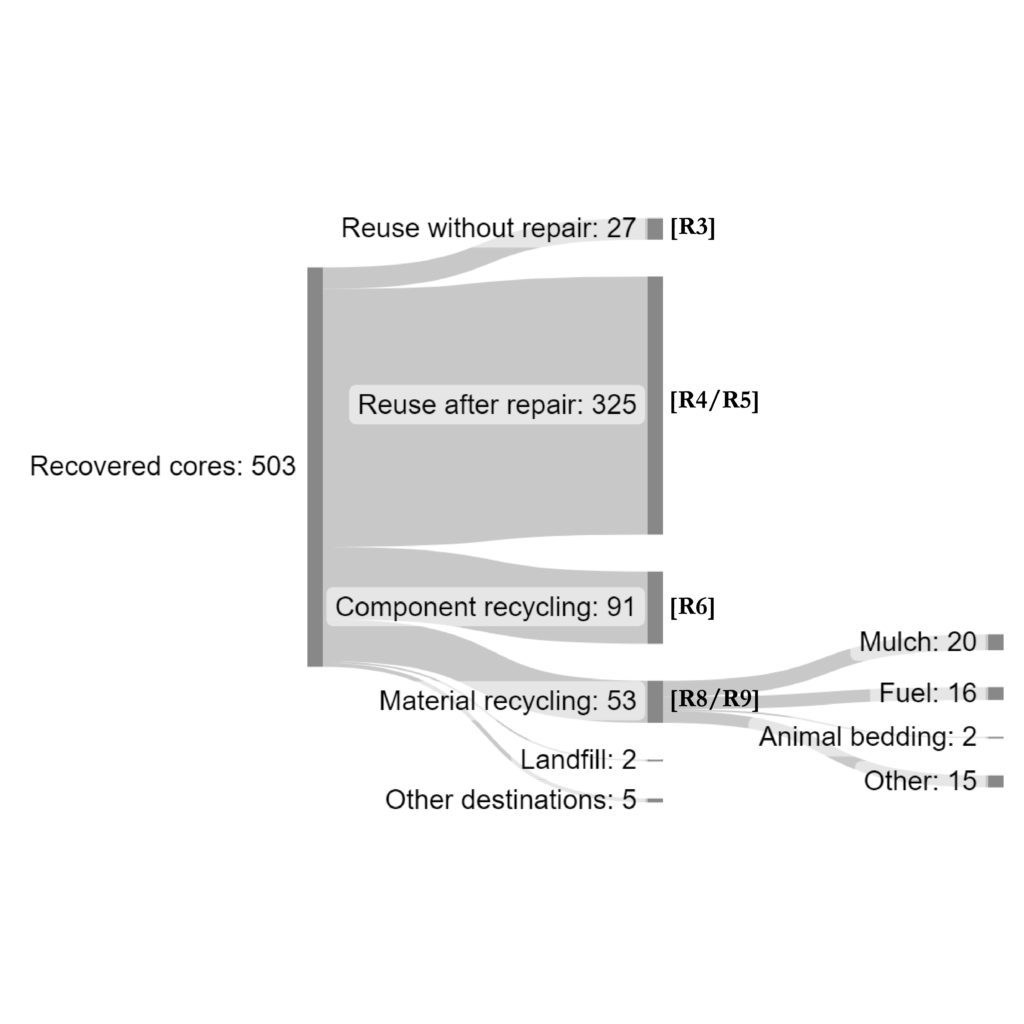
Figure 1‑4. Destinations of wood pallet cores recovered in the U.S. in 2016 (millions).
Data source: (Gerber et al., 2020)
Analysing these results under the R-framework, we can see that for the fraction of wood pallet cores which are recovered after use, R4, R5, and R6 practices are dominant. Following this, it is reasonable to assume that the wood packaging industry already exercises a high degree of circularity; indeed, pallet pooling organisations are commonly regarded as some of the most sustainable businesses operating today (Freijo, 2022). However, it is important to note that the mere occurrence of circular practices does not preclude the possibility of improvements to these practices using R1 and R2 interventions. This possibility has not been investigated strategically in any publication to date and is the central exploration of this research. While existing research in the field of packaging sustainability often lauds the returnable pallet as an exemplary circular product, this thesis instead examines how existing capacities for reuse and product life cycle extension in the wood packaging industry can be leveraged to further improve on a strong foundation for circularity.
Calculating the economic and environmental benefits of improved wood pallet management
A scenario analysis model was built in Excel that incorporates and expands upon Mollenkopf et al.’s relative cost approach for assessing the viability of one-way and returnable container systems, discussed in detail in Section 2.2. The model contributes to RO1 by assessing the economic and environmental benefits of the optimisation and adoption of returnable wood pallet systems.
This model was used to calculate the per-hire costs, timber consumption, steel consumption, and GHG emissions of five one-way and reusable wood pallet system alternatives at the scale of the individual packaging user using values derived from existing academic and trade literature on transport packaging systems as inputs. The functional unit is the “pallet hire;” which represents either the purchase of one single-use pallet or the rental of one returnable pallet for one use cycle. The system boundary for emissions, timber consumption, and steel consumption begins with raw materials at the new pallet manufacturer’s gate and ends at collection for EOL management.
These results were then aggregated to the scale of the entire U.S. wood pallet market according to the following three portfolios of pallet systems to generate estimates of the total economic and social value of the optimisation and increased adoption of returnable wood pallet systems throughout the United States:
I. Baseline: System [R]FTL comprises 25% of total U.S. annual hires, system [E]FTL comprises 22% of hires, and system [E]LTL comprises 53% of hires. This portfolio approximates the composition of the U.S. wood pallet market as of 2022.
II. Existing reuse improved: [R+]FTL comprises 25% of hires, [E]FTL comprises 22% of hires, and [E]LTL comprises 53% of hires. This portfolio represents a scenario in which the practices of returnable pallet systems are optimised for cost- and resource efficiency according to findings from academic literature, but returnable systems do not gain market share nor displace demand for one-way pallet systems.
III. Universal improved reuse: [R+]FTL comprises 47% of hires and [R+]LTL comprises 53% of hires. This portfolio represents a scenario in which the practices of returnable pallet systems are optimised for cost- and resource efficiency according to findings from academic literature, and returnable systems are universally adopted in place of one-way pallet systems.
“Social costs” in this case represent the indirect economic costs of resource consumption, and are calculated as a sum of the social costs of GHG emissions and the opportunity costs of timber and steel consumption. Figures for timber and steel consumption of different wood pallet systems were derived from a life cycle assessment of different reuse intensities of industrial wooden containers conducted in Spain (Gasol et al., 2008).
The potential of wood packaging to save the U.S. economy 20 Mt of carbon and $20 billion
The document below details the results of the model, aggregated to national scale across the roughly two billion wood pallets in circulation in the U.S. economy.
The results show that the following annual savings can be gained through better wood pallet reuse:
- $20.3 billion in producer operating expenses
- 25 million tonnes of industrial roundwood (10% of total U.S. consumption)
- 1.1 million tonnes of steel (1% of total U.S. consumption)
- 20 million tonnes of CO2 (0.4% of total U.S. emissions)
Discussion
There are clear economic and environmental cases for the push to improve and expand wood pallet reuse in the U.S. Organizations practicing in the wood packaging industry will need to collaborate in order to operate efficient reuse schemes at scale. Below is a list of activities the wood packaging industry should encourage according to the seven operational principles of circular economy:
- Adjusting inputs to the system to regeneration rates
There are finite technical and ecological limits to the volume of wood biomass which can be sustainably harvested for human use. Reducing the timber consumption of the wood packaging industry would make a significant fraction of this maximum sustainable harvest available for alternative purposes. - Adjusting outputs from the system to absorption rates
GHG emissions from wood packaging systems should be minimised to reduce the industry’s contribution to climate change. - Closing the system
Material leakage in the form of lost, damaged, and unviable secondhand product should be minimised. - Maintaining resource value within the system
Wood packaging should be kept in service for as long as possible, and material that is no longer usable should be cascaded down the value hierarchy in such that value durability is maximised. Wood material has a variety of technical, biological, and energy applications, and the same material can serve many of these functions in a sequence before it is finally disposed of. - Reducing the system’s size
Minimising the in-use stock of packaging by increasing its utilisation and minimising the distances over which the packaging must travel are key strategies to reduce the resource consumption of the wood packaging industry. - Designing for circular economy
Wood packaging which is designed for value durability and a high intensity of use will carry lower environmental burdens than that which is designed to meet an initial consumer’s specification at a minimum purchase price. - Educating for circular economy
Wood packaging manufacturers must be aware of best practices for design, procurement, manufacturing, transportation, repair, and EOL management of their products. Users must be aware of best practices for loading, handling, and reverse logistics of these products.
References
Related reading
- Wood Pallet Reuse: Best Practices
- Producer Responsibility in the Wood Packaging Industry
- Summary: Circular Transformation of the American Wood Packaging Industry